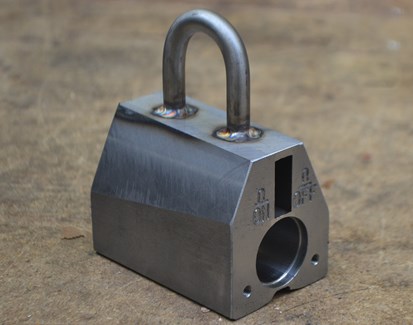
Einen hochwertigen Lasthebemagnet erkennt man an seiner geschweißten Konstruktion. Der Magnetkern eines Permanentmagneten besteht aus Neodym, das Herzstück des Elektromagneten ist eine elektrische Spule, Elektropermanentmagnete haben beides in sich. Werfen Sie einen Blick hinter die Kulissen der Magnetherstellung hier bei Walmag.
Wir bei Walmag nennen uns selbst einen Magnethersteller. Aber wenn wir genau sein wollen, sollten wir unseren Betrieb wie folgt beschreiben: Wir stellen Lasthebemagnete und Magnetspannplatten her. Das Wort „Magnet“ sollte eigentlich nur verwendet werden, um zu beschreiben, was Magnetismus als physikalisches Phänomen verursacht. Der Magnet selbst ist im Inneren verborgen und ist nur ein Teil des Geräts, das wir an den Kunden liefern.
Herstellung von Lasthebemagneten
1. Materialvorbereitung und Bearbeitung
Der erste Schritt ist die Vorbereitung des Materials – der Einzelteile, aus denen wir die Magnete zusammensetzen. Für die äußere Konstruktion verwenden wir Stahlteile. In den meisten Fällen handelt es sich um gezogenen Stahl, der aus Europa stammt. Wenn wir keinen Stahl in der erforderlichen Qualität von einem europäischen Hersteller bekommen können, sorgen wir dafür, dass er zumindest den europäischen Normen entspricht. Wir bearbeiten die Stahlteile auf CNC-Maschinen – zuerst formen wir die einzelnen Teile, dann schweißen wir sie zusammen.
Das Schweißen der äußeren Magnetkonstruktion ist ein sehr wichtiger Moment. Sie ist ein Spiegelbild der Magnetqualität – minderwertige Lasthebemagnete haben meist eine geschraubte Konstruktion. Sie halten niemals so viel aus wie ein geschweißter Magnet. Die verschraubten Teile lösen sich immer mit der Zeit und der Magnet beginnt im Wesentlichen auseinanderzufallen.
TIPP: Lesen Sie, wie hochwertiger Hebemagnet auf den ersten Blick erkennbar ist. |
2. Einsetzen der Magnete und ggf. der Steuereinheit
In die vorbereitete Außenkonstruktion des Lasthebemagneten fügen wir dann die übrigen Teile ein, die je nachdem, ob es sich um einen Permanentmagnet, Elektropermanentmagnet oder Elektromagnet handelt. Die Teile werden in die Magnetstruktur eingesetzt und mit Epoxid befestigt.
Permanente Lasthebemagnete haben mehrere Neodym-Magnete (die Anzahl hängt vom Produkt ab) und einen Rotor, der den Magnet schaltet. Je nachdem, ob der Magnet ein- oder ausgeschaltet ist, werden die Magnete im Inneren der Konstruktion so gedreht, dass ihr Magnetfeld ferromagnetische Lasten anzieht oder nicht anzieht.
Elektrische Lasthebemagnete haben eine Spule in sich, die magnetisch ist oder nicht, je nachdem, ob der Magnet unter Strom steht oder nicht. Wir bei Walmag stellen die Spulen selbst her.
Wenn der Magnet über eine Steuereinheit verfügt (Elektromagnete und Elektropermanentmagnete verfügen über eine solche Einheit, die elektronisch und nicht manuell gesteuert wird), besteht der nächste Produktionsschritt darin, die Elektronik zu montieren und zu überprüfen, ob alles wie gewünscht funktioniert.
3. Revision und Zertifizierung des Hebemagneten
Der nächste Schritt bei der Herstellung eines Lasthebemagneten ist die Überprüfung der Tragfähigkeit. Nach den geltenden Normen muss jeder Lasthebemagnet tatsächlich mindestens das Dreifache seiner Nenntragkraft tragen können – diese Eigenschaft wird durch den sogenannten Abreißtest geprüft. Bei Walmag erschweren wir diese Prüfung zusätzlich, indem wir ein Blatt Papier zwischen die zu hebende Last und die Auflagefläche des Magneten legen. Damit werden Luftspalten simuliert, wie sie in der Praxis oft vorkommen, z.B. durch eine unebene Oberfläche der angehobenen Last, zerkratzten Lack oder durch Staub und andere Schmutzpartikel. All diese Faktoren reduzieren die Magnetkraft und damit die tatsächliche Tragfähigkeit des Magneten. Unser Abreißtest gewährleistet, dass die tatsächliche Tragfähigkeit des Magneten mehr als das Dreifache der angegebenen Nenntragfähigkeit beträgt.
TIPP: Mehr über die Zertifizierung der Lasthebemagnete erfahren Sie im Artikel. Die Qualität der Lasthebemagnete ist auch im Hinblick auf die Sicherheit wichtig – minderwertige Magnete asiatischer Herkunft haben möglicherweise gar nicht die erforderlichen Zertifikate. |
4. Lackierung, Etikettierung, Versand
Nach dem Abreißtest, bei dem die Tragfähigkeit überprüft wird, geht der Magnet in die Lackiererei und anschließend in den Versand, wo die erforderlichen Etiketten (mit der Nenntragfähigkeit des Magneten und anderen obligatorischen Angaben) und anderes „Zubehör“ am Magnet angebracht werden (beispielsweise unser neuer REVOLIFT-Hebemagnet ist mit einem NFC-Chip ausgestattet, der einen elektronischen „Stammbaum“ des Magneten enthält, der einfach mit dem Smartphone abgerufen werden kann und es dem Mitarbeiter ermöglicht, z.B. die Anleitung für den Magnet in wenigen Sekunden nachzuschlagen). Der etikettierte und verpackte Magnet wird dann an den Kunden verschickt.
Herstellung von Magnetspannplatten
1. Materialvorbereitung und Bearbeitung
Der erste Schritt ist ähnlich wie bei den Lasthebemagneten – die Vorbereitung von Stahlplatten und anderen Materialien, die für die Herstellung von Lasthebemagneten benötigt werden. Unser Angebot an Magnetspannplatten ist breit gefächert, so dass das Material sehr unterschiedlich ist (Bleche für die Lamellen von Permanentmagneten, Stahl und Messing für die Herstellung von Polplatten usw.) Für jede Magnetspannplatte gibt es eine genaue Produktionsdokumentation.
Die Stahlteile werden dann auf CNC-Maschinen zur Herstellung der Magnetgrundplatte verwendet. Darauf montieren wir das magnetische Material – bei Permanentmagneten verwenden wir Lamellen, bei Elektropermanentmagneten und Elektromagneten montieren wir die Grundplatte mit Magneten in Größe und Dichte nach der jeweiligen Zeichnung.
2. Zubehör für Magnetspannplatten
Wird der Spannplatte eine Polplatte hinzugefügt, fräsen wir auch diese und bestücken sie anschließend mit Magneten nach Bedarf. Die montierte Magnetspannplatte wird anschließend auf einer CNC-Maschine endbearbeitet, bei lackierten Produkten in der Lackiererei lackiert und abschließend einer Ausgangskontrolle unterzogen.
Magnetspannplatten sind häufig mit einer Steuereinheit ausgestattet, die wir, wie bei den Lasthebemagneten, in der Endphase der Produktion in den Magneten einbauen. Die Spannplatte mit der Steuereinheit kann an die Bearbeitungsmaschine angeschlossen werden, so dass der Bediener in der Produktion dann sowohl die Bearbeitung als auch das Spannen auf einem Bildschirm steuert.
Im Gegensatz zu Lasthebemagneten gibt es für Magnetspannplatten keine einheitliche Magnetkraftprüfung. Bei Walmag testen wir die Magnetspannplatten, indem wir den Magnetfluss mit Geräten messen und den eigentlichen Abreißtest auf einer Prüfvorrichtung durchführen.
Wie lange dauert die Herstellung der Lasthebemagnete und Magnetspannplatten?
Die Herstellung eines Lasthebemagneten oder einer Magnetspannplatte dauert 4-6 Wochen. Wir haben unsere meistverkauften Modelle auf Lager, wir fertigen jedoch oft Sonderanfertigungen für Kunden an. Walmag hat eine eigene Entwicklung und Produktion – unsere Ingenieure entwerfen die Lasthebemagnete und Magnetspannplatten, während sie bei kundenspezifischen Magneten eng mit dem für den Kunden zuständigen Händler zusammenarbeiten. So haben wir z.B. das Magnetprisma (Form der Auflagefläche) oder den Schalthebel für Siemens in Frenštát pod Radhoštěm modifiziert.
Wenn Sie an unserer Produktion interessiert sind, zögern Sie nicht, uns zu kontaktieren – wir werden eine Lösung für Sie finden. Neben einzelnen Magneten können wir auch große Lasthebemagnetsysteme auf Bestellung herstellen.